The service and experience offered to customers can make or break a business. As much as no one wants to think about the potential catalysts that could lead to the demise of their business, customer expectations are at an all-time high – and if you do not deliver, the consequences could be severe.
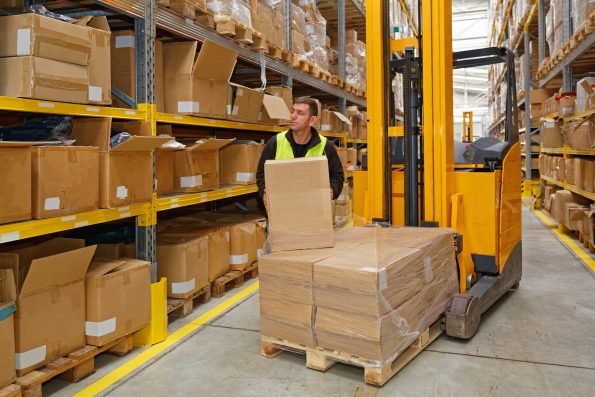
In eCommerce, proper order fulfillment is vital to attract and retain customers. No one wants to wait too long for their order or see it arrive damaged, so what can online companies do to improve their processes?
Below are five tips to improve your order fulfillment and, subsequently, your entire business:
- Inventory Accuracy
Inventory metrics might be a new phrase for you, but it is one that you must familiarize yourself with.
If your metrics are inaccurate, then your entire operation may as well shut down. Your teams must be able to properly store, pick, pack, and ship your orders in the quickest, safest way possible.
Customers, delivery partners, and employees must see what is in stock and available in real time. If your inventory is not accurate, it could lead to problems with backorders, deadstock, and stock-takes.
- Warehouse Layout
How your warehouse gets laid out significantly affects its efficiency.
Create a layout that optimizes workflow and prioritizes efficiency. That does not mean just for dispatch areas. Start from the first step of accepting inbound stock and work through to the final step before shipping it out.
There is much to consider for warehouse optimization, so get a professional to assist.
- Streamline Order Picking
Order picking is one of the most critical components of a distribution center.
Optimizing your pick and pack fulfillment is not rocket science, but it can be challenging if you are unfamiliar with your industry’s best practices. Streamlined order picking boosts the efficiency of the entire operation and gets products into the hands of your customers in record time.
- Reduce Handling
One of the most critical steps to improve your order fulfillment process is monitoring.
Monitor the average number of touches (handling time) a typical item in your warehouse gets exposed to. The more handling items go through, the more room there is for human errors and mishandling.
The result of overhandling could easily lead to the shipping of incorrect items, labeling errors, and damaged inventory. Reduce the number of times each product gets handled, and it will automatically boost the speed of your fulfillment process.
- Minimize Packaging
Online retail is synonymous with overpackaging.
How many times have you received an order only to find that some items came from different locations, resulting in individual boxes for each item?
Every e-commerce business looking to improve efficiency should prioritize using the least amount of packaging possible. More packaging is not only the opposite of sustainable – but it also means more handling and waste.
Figure out the ideal amount of packaging to protect your items in transit, using the least number of materials.
To End
Remember that learning the best practices in your industry will help establish and improve strategies, share performance metrics, and ensure that everyone is on the same page so that your inventory gets replenished on time and your orders get dispatched efficiently.